LABORATORY FUME HOODS |
|||||||||
(contract last updated 12/01/2021) | |||||||||
SCOPE: Low Velocity fume hoods for use in laboratories and research areas in various campus locations. Prior approval from the Division of Facilities Planning and Management is required prior to any work that impacts the mechanical and electrical system of a campus building, including installation of equipment. | |||||||||
CONTRACT # | DESCRIPTION | ||||||||
21-5763 | LABORATORY FUME HOODS | ||||||||
CONTRACT ORIGIN: | ADDITIONAL INFORMATION: | ||||||||
UW-Madison Purchasing Services 21 N Park St, Ste 6101 Madison, WI 53715-1218 |
UW-Madison users contact: Brad Bauman (608) 262-1327 FAX (608) 262-4467 brad.bauman@wisc.edu |
||||||||
Non-UW-Madison users contact: Vendor Representative | |||||||||
SPECIAL APPROVAL REQUIRED FROM: |
Division of Facilities Planning and Management Fume Hood Committee |
||||||||
|
RISK MANAGEMENT DEPARTMENT Vendor’s Insurance Certificate must be on file when inside delivery or setup is requested. |
||||||||
COOPERATIVE PURCHASING: | YES | ||||||||
CONTRACT TERM: | May 1, 2021 through April 30, 2024, with automatic renewal extensions to April 30, 2026, unless amended, cancelled or rebid. |
||||||||
| |||||||||
Revision History: |
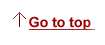